Over 90 years of tradition and innovation have made ASKUBAL a defining brand. Now in its fourth generation, the owner-managed family business is ideally equipped for the future.
A Traditional Company with a Vision for Innovation
At ASK Kugellagerfabrik, we have been setting standards in precision manufacturing for four generations. Our commitment is to excel in all areas – a philosophy deeply rooted in our corporate culture. Our flexible production facility in Stuttgart is at the heart of this mission, enabling us to efficiently produce over 6000 standard designs as well as specialized, customer-specific solutions today.
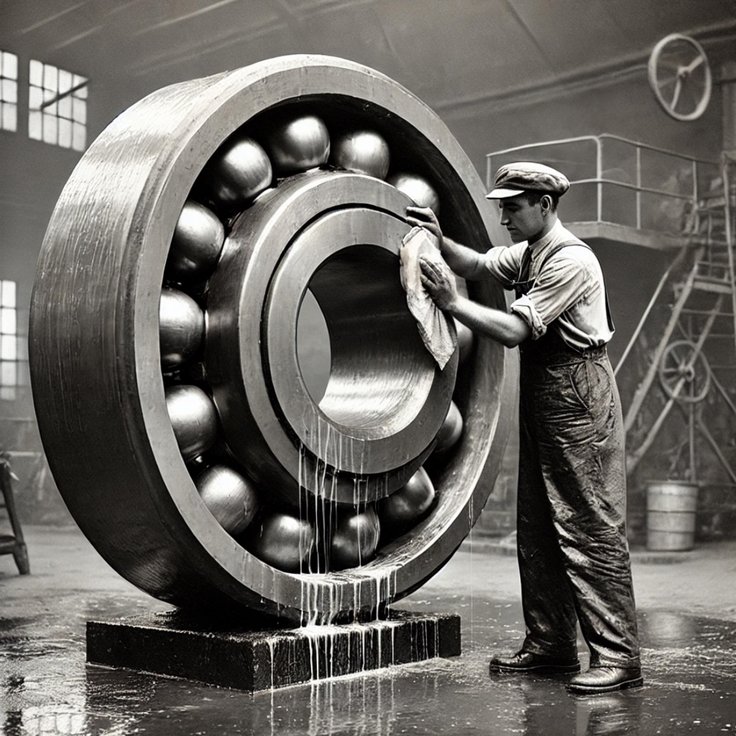
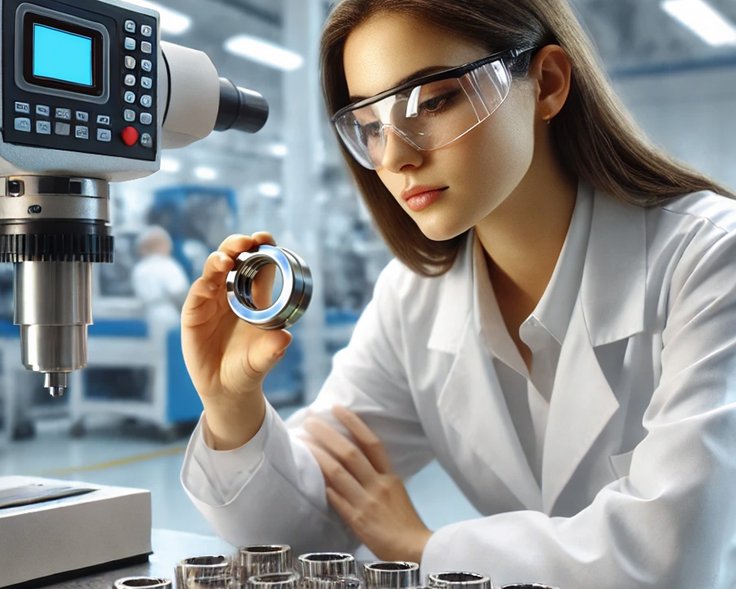
Customized solutions and just-in-time delivery
Our ability to precisely implement individual customer requirements is what sets us apart. Thanks to our deep understanding of the requirements of specific industries and close collaboration with our customers, we can deliver both standard products and special parts efficiently and to exact specifications. Our just-in-time production strategy underlines our flexibility and commitment to customer satisfaction and operational efficiency.
Rooted in Stuttgart, in use worldwide
The quality of our products and our innovative production process have enabled us to maintain a firm foothold in the global industry. Based in Stuttgart, we operate worldwide to meet the constantly growing and evolving requirements of our international clientele.
Dr. Roland Seyfert

In 1930, Artur Seyfert made the entry in the commercial register. In the same year, Bickelhaupt GmbH was founded. A Stuttgart company specializing in special ball bearings and engine parts, which was taken over by the Seyfert family about 15 years later.

In November 1934, a new rolling bearing technology was developed that met with great success in the industry. Today, even more than back then, the ASK Ball Bearing Factory is always kept at the cutting edge of technology by bearing specialists with a creative inventive spirit. The creativity required for this is encouraged and exemplified by the executive management.

After his studies and subsequent doctorate at the University of Tübingen, the entrepreneur Dr. Roland Seyfert (in the picture) founded the ball bearing wholesale Artur Seyfert KG together with his father.
Step by step, the two generations combine the know-how of the ball bearing factories located in the Stuttgart region at that time, concentrating on one central location.
By using the latest technologies for their own machinery, a strong, technically oriented team and the constant thirst for progress through knowledge and experience, Dr. Roland Seyfert sets further decisive milestones in the history of ASK as a manufacturer.

As ASK Kugellagerfabrik GmbH, the company produces the wide range of rolling bearings and special parts for mechanical engineering at its location in Stuttgart. The large distributor network, which is still maintained today, ensured the strong, worldwide distribution of ASK quality bearings even back then.

In addition to the production of rolling bearings, new types of rod ends and spherical plain bearings with adjustable bearing clearance were developed, patented and put into production.

ASK becomes exclusive distributor for ASAHI housing units. With this step, the existing "High-Quality" rolling and plain bearing product portfolio could be extended by Japanese quality housing units.

ASK becomes the exclusive distributor for McGill metric cam follower bearings. This step rounds off the product variety for the most complex, technical issues. The entire ASK know-how has been focused on rolling and plain bearing technology since 1930. Therefore, the company only offers products that have been developed according to German experience.

In 1994, the company was certified according to DIN EN ISO 9001 for the first time. At ASK, the executive management acts as a pioneer in terms of quality and creates the conditions for implementing even the most complex customer requirements with the utmost care.
In addition to the DIN EN ISO 9001 certification, in-house company standards are developed for the continuous improvement of our products and processes.

In 1995, principles of lean management were introduced and through this, the continuous improvement process "Kaizen" was integrated throughout the company. The Japanese philosophy is still practiced at ASK today and integrated into the company's daily routine through regular training.
The success of Kaizen is reflected in the high flexibility and the constant optimization of set-up and production times.

Implementation of SAP R3.

In 2007 our company expanded through improvements and the addition of a fully automated small parts warehouse.
This step allows ASK to access more than 6000 standard and special parts as quickly as possible, according to the 0-error principle.

Since 2008, the company has been certified according to DIN EN ISO 14001 environmental management.

As part of our responsibility to the environment and to ensure the security of our processes, ASK has made a company-wide switch to a paperless, digital management system.

Development of a new liner technology for the maintenance-free spherical plain bearings and rod ends for the ASK Motorsport series.

4 generations, 88 years and around 100 employees:
ASK Kugellagerfabrik has been run by the family since its foundation, with 100% of the shares held. ASK's success results from the ambition and inquisitiveness of our team of almost 100 people.
Together we produce and distribute worldwide more than 6000 different serial and special parts according to customer requirements. And that just in time.